Czy można położyć gładź na gładź?
Marzenie o idealnie gładkich ścianach często zderza się z prozą budowlanej rzeczywistości – kurzem, nierównościami i wieloma godzinami pracy. Czy da się przyspieszyć ten proces, a jednocześnie uzyskać perfekcyjny efekt? Czy nakładanie kolejnych warstw materiału to konieczność czy sztuka? Przed malowaniem, kluczowe staje się jedno pytanie, które wraca niczym bumerang w świecie wykończeń wnętrz: czy można położyć gładź na gładź? Krótka odpowiedź brzmi: tak, co więcej, to często nieodłączny element dążenia do prawdziwie lustrzanej powierzchni, ale sukces tkwi w zrozumieniu specyfiki procesu.
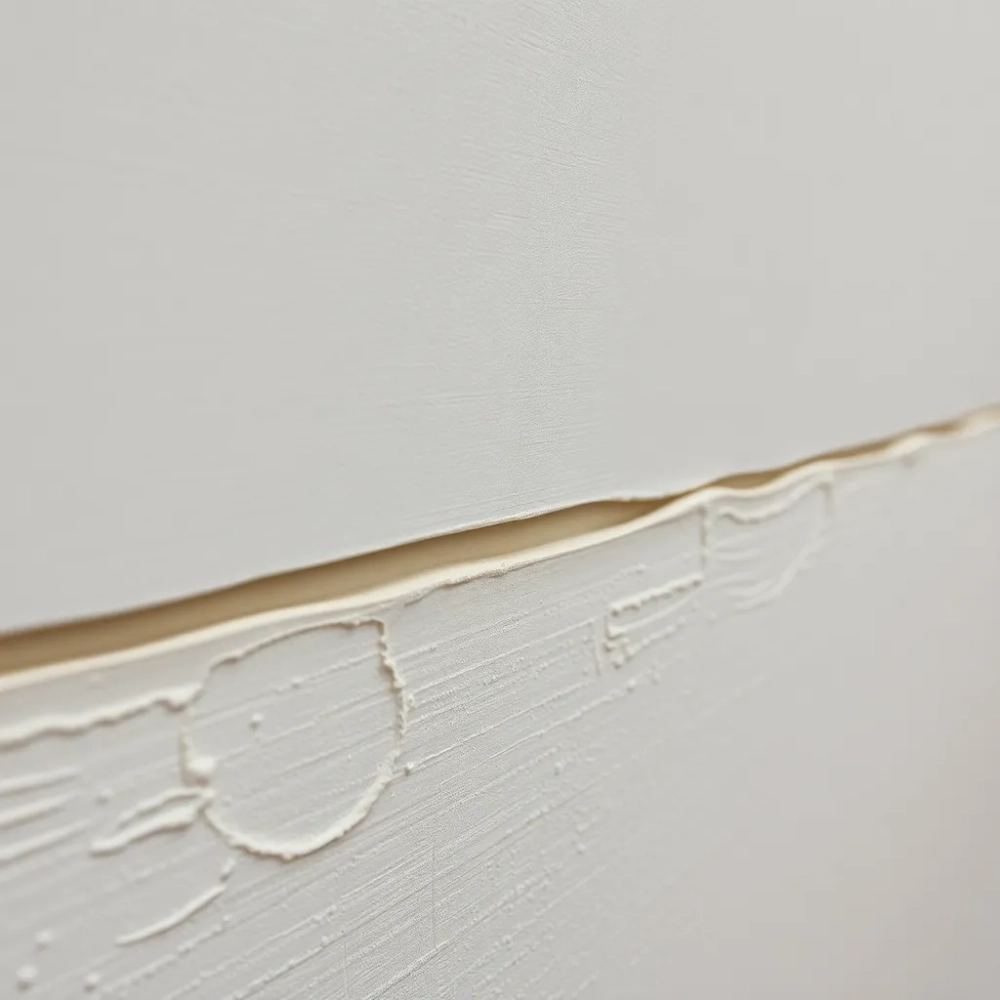
Tak, można położyć gładź na gładź
Odpowiedź na pytanie, czy można kłaść gładź na już istniejącą warstwę gładzi, jest zdecydowanie twierdząca, co więcej, jest to rutynowa praktyka w profesjonalnym wykończeniu wnętrz, stanowiąca często klucz do osiągnięcia tego wymarzonego, nieskazitelnie gładkiego podłoża, które stanowi idealną bazę dla farby, tapety czy innego wykończenia. Wykończeniowcy, którzy zjedli zęby na tysiącach metrów kwadratowych ścian, doskonale wiedzą, że uzyskanie efektu, o którym marzą architekci i inwestorzy – powierzchni tak równej i gładkiej, że światło ślizga się po niej bez ujawniania cienia nierówności – prawie zawsze wymaga aplikacji przynajmniej dwóch warstw materiału wygładzającego, a niejednokrotnie i więcej. Decydujący wpływ na to, ile dokładnie warstw gładzi szpachlowej ostatecznie znajdzie się na ścianie czy suficie i jak spektakularny będzie finalny efekt, ma oczywiście stan pierwotnej powierzchni, na którą ma być nałożona pierwsza warstwa masy – im więcej niedoskonałości, tym więcej pracy i materiału będzie potrzebne do ich skorygowania. Stan istniejącej gładzi, na którą planujemy aplikację kolejnych warstw, jest absolutnie krytyczny dla powodzenia całego przedsięwzięcia; mówiąc kolokwialnie, nie da się zbudować solidnego dachu na trzęsących się fundamentach.
Aby kolejne warstwy mogły właściwie związać się z podłożem i spełnić swoje zadanie – doprowadzić powierzchnię do perfekcyjnej gładkości i wyrównać wszelkie drobne pęknięcia, ubytki czy nierówności, które mogły powstać na pierwszej warstwie podczas schnięcia czy lekkiego osiadania materiału – podstawa musi być stabilna, czysta i odpowiednio przygotowana. To nie jest zadanie dla gładzi położonej na "odczepnego", pełnej rys, pęknięć, kurzu, tłustych plam czy resztek starych klejów, które nie tylko pogorszą przyczepność nowego materiału, ale mogą także prowadzić do nieestetycznych przebarwień lub co gorsza, do łuszczenia się całej nowej powłoki w przyszłości. Profesjonalne podejście nakazuje dokładne ocenienie stanu istniejącej gładzi: sprawdzenie jej przyczepności do podłoża (czy nigdzie się nie odspaja, nie puchnie), stopnia jej chłonności (czy nie "pije" wilgoci z nowej warstwy zbyt szybko lub zbyt wolno), usunięcie wszelkich luźnych cząstek, kurzu i brudu, a w przypadku stwierdzenia znaczących defektów, podjęcie decyzji o konieczności wykonania gruntowniejszych napraw lub nawet, w skrajnych przypadkach, usunięcia starej warstwy i zaczęcia pracy od podstaw – tak, jak uczy doświadczenie, lepiej zainwestować czas w solidne przygotowanie, niż później borykać się z problemami, które zrujnują estetykę i trwałość finiszu. W przypadku, gdy istniejąca gładź jest w dobrym stanie, równa i mocno związana z podłożem, wystarczy zazwyczaj lekkie przeszlifowanie jej powierzchni w celu usunięcia ewentualnych zadziorów czy resztek zabrudzeń, a następnie bardzo dokładne odpylenie całej płaszczyzny – ten drobny krok, choć często niedoceniany, ma gigantyczne znaczenie dla adhezji kolejnej warstwy, gwarantując, że nowo nałożony materiał połączy się z poprzednim "na amen", tworząc jednolitą i wytrzymałą powłokę, gotową na finalne wykończenie i eksponowanie w pełnym blasku światła.
Zarówno teoretycznie, jak i praktycznie, nakładanie gładzi na gładź nie tylko jest możliwe, ale stanowi kamień węgielny dążenia do idealnej płaszczyzny ścian i sufitów, która jest przecież celem każdego, kto bierze się za kompleksowe wykończenie wnętrza lub renowację, chcąc uzyskać efekt daleki od amatorskich prób, a bliski poziomowi artystycznego rzemiosła. Minimum dwie warstwy to swoisty branżowy standard, swego rodzaju "higieniczne minimum" akceptowalne w większości sytuacji, pozwalające na skorygowanie defektów, które są nieuniknione podczas pracy z tak wymagającym materiałem, jakim jest masa szpachlowa, a które wynikają chociażby z naturalnego skurczu wiążącego materiału, sposobu prowadzenia narzędzia (pacy czy agregatu), czy nawet mikroskopijnych zanieczyszczeń powietrza osiadających na świeżej warstwie. To właśnie druga warstwa gładzi, nakładana z precyzją i wyczuciem na odpowiednio przygotowaną (i w zależności od metody, całkowicie suchą lub jedynie podeschniętą) pierwszą powłokę, pozwala nadać powierzchni tę ostateczną, aksamitną gładkość, której nie da się osiągnąć przy jednorazowej aplikacji – działa jak papier ścierny o najwyższej gradacji w połączeniu z idealnym wypełniaczem, niwelując najdrobniejsze ryski po pace, wyrównując minimalne różnice w poziomie i fakturze, a także zamykając pory materiału, co przekłada się na równomierną chłonność podłoża przed malowaniem, eliminując ryzyko powstawania plam czy pasm po farbie. Oczywiście, na perfekcję wpływa nie tylko liczba warstw, ale przede wszystkim umiejętności osoby wykonującej pracę – doświadczony specjalista potrafi ocenić stan podłoża, dobrać odpowiedni materiał (gotowa masa polimerowa, gładź gipsowa szpachlowa czy finiszowa, produkty szybkoschnące) i metodę aplikacji (ręczna, maszynowa, na mokro) w taki sposób, aby minimalnym nakładem pracy i materiału uzyskać maksymalnie satysfakcjonujący efekt, co w efekcie oszczędza czas i pieniądze, ale przede wszystkim, eliminuje frustrację związaną z poprawkami czy niezadowalającym rezultatem końcowym.
Wartościowe dane, wyłuskane z opinii wielu wykonawców i analiz kart technicznych produktów, wskazują na konkretne parametry aplikacji, które są wyznacznikiem profesjonalizmu w dziedzinie kładzenia gładzi na gładź. Standardowa grubość pojedynczej warstwy gładzi finiszowej rzadko przekracza 2-3 mm – jest to celowy zabieg podywkowany kilkoma względami technicznymi. Po pierwsze, grubsze warstwy wiążą się z większym skurczem, co znacząco zwiększa ryzyko powstawania rys i pęknięć, zwłaszcza przy szybkim schnięciu; cienka warstwa kurczy się minimalnie, jest elastyczniejsza i lepiej przylega do podłoża bez naprężeń. Po drugie, nałożenie zbyt grubej warstwy ręcznie za pomocą pacy jest znacznie trudniejsze, grozi powstaniem większych nierówności i wymagałoby znacznie więcej pracy podczas szlifowania, generując też znacznie więcej pyłu. Po trzecie, materiał schnie od powierzchni w głąb – grubsza warstwa może być sucha na zewnątrz, ale mokra w środku, co stwarza problemy przy szlifowaniu i nakładaniu kolejnych warstw, a także przy malowaniu (wilgoć uwięziona pod farbą może prowadzić do jej odspojenia lub powstawania pęcherzy). Dlatego właśnie, nawet na względnie równym podłożu, pojedyncza cienka warstwa (np. 2 mm) rzadko zapewnia pełne, jednorodne krycie, ukrycie wszystkich subtelnych defektów (np. delikatnie widocznych łączeń GK czy śladów po wcześniejszych naprawach) i stworzenie idealnie gładkiej, matowej, jednolitej pod kątem chłonności powierzchni. Zwykle potrzeba drugiej warstwy, która niejako "doszlifuje" optycznie i strukturalnie pracę wykonaną podczas pierwszego przejścia, a niejednokrotnie, na bardzo wymagających powierzchniach lub przy restrykcyjnych wymaganiach dotyczących gładkości (np. pod malowanie natryskowe o wysokim połysku w pomieszczeniu o silnym oświetleniu bocznym), stosuje się nawet trzecią, ultracienką warstwę (tzw. "szpachlowanie na zero"), kładzioną szeroką pacą, aby finalnie wyeliminować absolutnie wszelkie mikroskopijne niedoskonałości. Takie metody, wypracowane przez pokolenia fachowców, są odpowiedzią na fizyczne i chemiczne właściwości materiałów budowlanych i są nieodzowne dla osiągnięcia standardów wykończenia premium.
Dlaczego zwykle nakłada się więcej niż jedną warstwę gładzi?
Głębokie zrozumienie procesu kładzenia gładzi wymaga spojrzenia na sam materiał i jego fizyczne ograniczenia – to właśnie one determinują konieczność aplikacji wielowarstwowej. Masa szpachlowa, w przeciwieństwie do tynku, który jest zaprojektowany do tworzenia stosunkowo grubych warstw (od kilku milimetrów do kilku centymetrów) i wypełniania dużych nierówności strukturalnych podłoża, jest materiałem przeznaczonym do aplikacji cienkowarstwowej, typowo w zakresie od ułamka milimetra do maksymalnie 2-3 milimetrów na jedno przejście, a nawet mniej w przypadku mas polimerowych, co wynika bezpośrednio z jej składu chemicznego, który minimalizuje skurcz wiążący. Próba nałożenia jednorazowo grubszej warstwy, na przykład 5-6 milimetrów, przy użyciu standardowej gładzi finiszowej niemal gwarantuje problemy: materiał będzie pękał podczas wysychania (zwłaszcza wzdłuż brzegów i na większych powierzchniach), będzie schnął nierównomiernie, co utrudni szlifowanie, a co najgorsze, może odspajać się od podłoża ze względu na nadmierne naprężenia wewnętrzne powstające podczas wiązania. Zatem, fundamentalnym powodem, dla którego zwykle nakłada się więcej niż jedną warstwę gładzi, jest fizyczna charakterystyka materiału, który ze względów technologicznych musi być aplikowany cienko, a jedna tak cienka warstwa, nawet położona przez mistrza pacy, po prostu nie jest w stanie w pełni wyrównać wszystkich subtelnych niedoskonałości i ukryć wszelkich przebarwień czy cieni na powierzchni.
Pojedyncza aplikacja, choć kusi perspektywą szybkiego zakończenia prac, w większości przypadków – szczególnie gdy podłoże nie jest absolutnie perfekcyjne – nie przynosi zamierzonych rezultatów estetycznych, pozostawiając na powierzchni subtelne wady, które staną się widoczne po pomalowaniu, zwłaszcza farbą o półmatowym lub matowym wykończeniu, nie mówiąc już o farbach satynowych czy z połyskiem, które są jak bezlitosne soczewki, potęgujące widoczność każdej najdrobniejszej ryski czy fale na ścianie. W realnym świecie budowlanym, powierzchnia, na którą kładzie się gładź, rzadko jest nieskazitelna – może to być płyta gipsowo-kartonowa z widocznymi, spoinowanymi taśmą połączeniami, stary tynk ze szwami i drobnymi pęknięciami, czy nowo położony tynk maszynowy, który, mimo wstępnego wyrównania, wciąż posiada pory, nierówności i często wymagające dopracowania narożniki; nawet stare powłoki malarskie, które zostały jedynie zmatowione, mogą mieć ubytki czy rysy. W takim kontekście, rola i funkcja pierwszej warstwy gładzi jest przede wszystkim techniczna i sprowadza się do: po pierwsze, gruntownego wyrównania ogólnej płaszczyzny ścian i sufitów – wypełnienia głębszych zagłębień, zakrycia taśm spoinowych na GK w taki sposób, aby ich struktura stała się niewidoczna, czy też zniwelowania szwów i różnic w poziomie tynków. Po drugie, pierwsza warstwa gładzi służy do wyprowadzenia i wzmocnienia krawędzi w narożnikach wewnętrznych i zewnętrznych, często z zastosowaniem kątowników aluminiowych lub papierowych, co zapewnia ich prostoliniowość i odporność na uszkodzenia mechaniczne. I po trzecie, stanowi ona pierwsze "zamknięcie" struktury podłoża, wstępnie je ujednolicając pod kątem chłonności i zapewniając spójną, chropowatą bazę dla kolejnych aplikacji, ale zazwyczaj sama w sobie wciąż jest zbyt niedoskonała pod kątem gładkości, aby służyć jako warstwa finalna.
Można by to porównać do pracy rzeźbiarza – pierwsze uderzenia dłutem mają na celu usunięcie dużych bloków materiału i nadanie ogólnego kształtu bryle; nie są one precyzyjne i pozostawiają szorstką, nierówną powierzchnię. Dopiero kolejne, delikatniejsze pociągnięcia, a na końcu szlifowanie drobnoziarnistym papierem ściernym, prowadzą do wydobycia subtelnych detali i osiągnięcia idealnej gładkości finiszu. Podobnie jest z gładzią: pierwsza warstwa "usuwa" największe wady i "kształtuje" ogólną płaszczyznę, druga warstwa (a czasem i kolejne) wchodzi w rolę drobniejszego szlifowania i dopracowywania detali. Grubości nakładanych warstw, które oscylują wokół 2-3 mm, są wynikiem starannego balansu między szybkością pracy, ryzykiem pękania materiału a efektywnością niwelowania nierówności – jest to optymalny zakres, który pozwala na skorygowanie defektów o średniej wielkości bez generowania nadmiernych naprężeń wewnętrznych. Ważne jest też, że każda kolejna warstwa gładzi pozwala na skorygowanie subtelnych błędów popełnionych podczas poprzedniego przejścia, takich jak drobne ryski od krawędzi pacy, niewielkie wgłębienia czy delikatne zgrubienia materiału – druga warstwa, rozprowadzana cienko na powierzchni pierwszej, działa jak korektor, wypełniając mikroskopijne nierówności i tworząc jednolitą płaszczyznę, która jest znacznie łatwiejsza i szybsza w szlifowaniu do ostatecznej gładkości, niż próbka szlifowania grubej, nierównej warstwy położonej "na raz". Co więcej, nawet na nowej płycie gipsowo-kartonowej, gdzie z pozoru wystarczyłoby jedynie zaszpachlować połączenia, nałożenie dwóch pełnych warstw gładzi finiszowej na całej powierzchni jest zalecane, a wręcz konieczne, aby wyrównać fakturę całej płyty z fakturą szpachlowanych połączeń, eliminując w ten sposób ryzyko, że po malowaniu widoczne będą pasma o innej chłonności lub subtelnie innej teksturze, ujawniające granice szpachlowanych obszarów. Jest to kwestia nie tylko estetyki, ale i trwałości – poprawnie wykonany, wielowarstwowy system gładzi jest bardziej odporny na mikropęknięcia wynikające z ruchów konstrukcji budynku czy zmian temperatury i wilgotności.
Kładzenie kolejnej warstwy gładzi po wyschnięciu pierwszej
Jedną z najczęściej stosowanych i uchodzących za najbardziej "bezpieczną" dla mniej doświadczonych wykonawców metodą kładzenia kolejnych warstw gładzi jest technika wymagająca zachowania pełnych przerw technologicznych między kolejnymi aplikacjami, co w praktyce oznacza czekanie, aż poprzednia warstwa materiału całkowicie wyschnie i stwardnieje, osiągając stabilność niezbędną do nałożenia następnej powłoki bez ryzyka jej uszkodzenia lub rozmoczenia spodniej warstwy. Proces ten jest dosyć intuicyjny: po nałożeniu pierwszej warstwy gładzi, rozprowadzamy ją równomiernie pacą lub agregatem, starając się wstępnie wyrównać powierzchnię i usunąć największe nierówności, a następnie pozostawiamy ją do pełnego wyschnięcia. Czas, po którym można przystąpić do nałożenia drugiej warstwy gładzi, jest zmienny i uzależniony od szeregu czynników, które każdy wykonawca musi wziąć pod uwagę, a jak szybko schnie gładź to pytanie kluczowe dla planowania pracy i dotrzymania terminów. Po wyschnięciu pierwszej warstwy, która powinna być jasna i twarda, przystępujemy do nałożenia kolejnej powłoki, która ma za zadanie udoskonalić powierzchnię, wyeliminować drobne defekty pozostałe po pierwszym przejściu i doprowadzić ścianę lub sufit do stanu bliskiego perfekcji. Proces ten, choć wymaga cierpliwości i wydłuża czas realizacji w porównaniu do metody "na mokro", minimalizuje ryzyko błędu i pozwala na dokładną ocenę pierwszej warstwy przed nałożeniem następnej, dając możliwość ewentualnych drobnych korekt czy oczyszczenia powierzchni z pyłu po częściowym szlifowaniu, jeśli zostało ono wykonane między warstwami.
Szacowanie czasu wysychania gładzi wymaga pewnego doświadczenia i wyczucia materiału, ale istnieją pewne ogólne wytyczne, które mogą służyć za punkt odniesienia: pojedyncza warstwa gładzi gipsowej, nałożona w typowej dla finiszowania grubości około 2-3 mm na chłonnym podłożu (np. płycie g-k czy suchym tynku), schnie zazwyczaj około kilku do kilkunastu godzin w optymalnych warunkach, co oznacza temperaturę powietrza wynoszącą około 20°C i wilgotność względną nieprzekraczającą 60-65% oraz zapewniony przepływ powietrza (bez przeciągów, ale z wentylacją). Te warunki są idealne dla większości materiałów budowlanych i sprzyjają równomiernemu i kontrolowanemu procesowi wiązania i odparowywania wody; niestety, w realnych warunkach budowlanych rzadko są one w pełni osiągalne przez cały czas. Grubość nałożonej masy ma oczywiście bezpośredni wpływ na czas schnięcia – grubsza warstwa (np. 5 mm) będzie schnąć znacznie dłużej, nawet 24 godziny lub więcej, a co gorsza, może być sucha na wierzchu, ale wciąż mokra w głębi, co może prowadzić do problemów, gdy zbyt wcześnie zaczniemy ją szlifować (szybko zapychający się papier ścierny) lub nakładać na nią kolejną warstwę (ryzyko rozmiękczenia spodniej warstwy lub gorszej adhezji). Wilgotność powietrza w pomieszczeniu jest bodaj najważniejszym czynnikiem spowalniającym schnięcie – w nowo wybudowanym, jeszcze wilgotnym domu czy w deszczową pogodę przy zamkniętych oknach, czas schnięcia może wydłużyć się dwukrotnie, a nawet trzykrotnie, osiągając 24 godziny lub więcej dla cienkiej warstwy; w takich warunkach kluczowe jest zapewnienie wentylacji i ewentualne zastosowanie osuszaczy powietrza. Temperatura również odgrywa rolę – niższa temperatura (np. 10-15°C) spowolni proces schnięcia, natomiast zbyt wysoka temperatura (powyżej 25°C) lub silne słońce padające na ścianę mogą spowodować zbyt szybkie odparowywanie wody z powierzchni, prowadząc do powstawania mikrorys, skurczu i obniżenia wytrzymałości warstwy. Zatem, aby prawidłowo nałożyć drugą warstwę gładzi metodą "sucho na sucho", niezbędne jest sprawdzenie stanu pierwszej warstwy – powinna być ona twarda, jednolita pod kątem koloru (bez ciemniejszych, wilgotnych plam) i nie powinna "kleić się" ani uginać pod naciskiem narzędzia czy palca; profesjonaliści często delikatnie szlifują pierwszą warstwę przed nałożeniem drugiej, aby usunąć drobne zgrubienia i zadziory oraz zapewnić lepszą adhezję.
Kwestia odpowiedniej przerwy technologicznej między warstwami, gdy stosujemy tradycyjną metodę, jest na tyle istotna, że ignorowanie jej może pogrzebać cały projekt i doprowadzić do konieczności żmudnych poprawek, a nawet zerwania wadliwych warstw – jest to częsty błąd niedoświadczonych majstrów, którzy chcą przyspieszyć proces za wszelką cenę, nie zdając sobie sprawy z konsekwencji, że materiały budowlane rządzą się własnymi, nieubłaganymi prawami fizyki i chemii. Kiedy pierwsza warstwa jest sucha, powierzchnia jest zazwyczaj matowa, jednolita kolorystycznie (przybierając barwę typową dla suchej gładzi, często białą lub lekko kremową, w zależności od producenta i typu produktu) i twarda w dotyku; delikatne przejechanie po niej pacą szpachlową nie powinno pozostawiać żadnych śladów ani rys. Jeśli po przejechaniu pacą pozostają wilgotne ślady lub materiał "zbiera się" pod narzędziem, oznacza to, że warstwa nie wyschła jeszcze w pełni i należy poczekać – pójście dalej w takiej sytuacji to proszenie się o kłopoty. Warto pamiętać, że różne rodzaje gładzi (gipsowe tradycyjne, polimerowe, gotowe masy akrylowe, gładzie cementowe) mają różny czas wiązania i schnięcia, podyktowany ich składem chemicznym i zawartością wody, dlatego zawsze, ale to absolutnie zawsze, należy zapoznać się z zaleceniami producenta podanymi na opakowaniu produktu lub w karcie technicznej; czas schnięcia gładzi podawany przez producenta jest zazwyczaj wartością szacunkową, dotyczącą optymalnych warunków i średniej grubości warstwy, więc w rzeczywistości może być inny. Metoda "sucho na sucho" daje większą kontrolę nad procesem, ponieważ widać dokładnie, jak prezentuje się pierwsza warstwa po wyschnięciu – pozwala to na ewentualne, niewielkie poprawki przed nałożeniem następnej powłoki, a także minimalizuje ryzyko, że nowa warstwa, która również zawiera wodę, wpłynie negatywnie na strukturę spodniej warstwy. Ta tradycyjna technika jest szczególnie polecana w przypadku pracy z gładziami tradycyjnymi, wymagającymi zarobienia z wodą, gdzie proces wiązania i odparowywania wody przebiega wolniej i jest mniej "kontrolowany" niż w przypadku nowoczesnych gładzi polimerowych czy szybkoschnących, które często umożliwiają aplikację w krótszych odstępach czasu lub nawet metodą "na mokro".
Nakładanie gładzi metodą "na mokro"
Metoda gładzenia ścian określana jako "na mokro" to technika, która w ostatnich latach zyskała na popularności, głównie ze względu na potencjalne znaczące skrócenie czasu potrzebnego na wykończenie powierzchni i możliwość uzyskania niezwykle gładkiego finiszu z minimalną ilością szlifowania, a czasem nawet bez konieczności używania papieru ściernego wcale. Polega ona na nałożeniu drugiej warstwy gładzi nie po jej całkowitym wyschnięciu, lecz w momencie, gdy pierwsza warstwa jest już częściowo związana i ustabilizowana, ale wciąż zawiera na tyle dużo wilgoci, że pozostaje elastyczna i podatna na obróbkę – jest to moment krytyczny, wymagający wyczucia i doświadczenia. Nakładanie gładzi metodą na mokro opiera się na wykorzystaniu specyficznych właściwości niektórych nowoczesnych mas szpachlowych, często opartych na żywicach polimerowych lub zmodyfikowanym gipsie, które pozwalają na chemiczne wiązanie kolejnych warstw zanim ta spodnia w pełni wyschnie, tworząc niejako jednorodną powłokę. Kluczem jest tu złapanie odpowiedniego momentu: pierwsza warstwa nie może być ani zbyt mokra (grozi to rozmiękczeniem i uszkodzeniem jej struktury przez narzędzie do aplikacji kolejnej warstwy oraz pogorszeniem przyczepności), ani zbyt sucha (wtedy metoda "na mokro" przestaje działać, a próbka jej zastosowania może prowadzić do powstania rys czy odspajania nowej warstwy). To trochę jak z pieczeniem ciasta – wyjęcie go z pieca zbyt wcześnie skończy się zakalcem, zostawienie zbyt długo w piecu spowoduje, że będzie suche jak wiór, a jedynie idealnie wyczuty moment pozwoli uzyskać puszystą konsystencję; podobnie z gładzią "na mokro", złapanie odpowiedniego momentu plastyczności pierwszej warstwy jest decydujące.
Przed przystąpieniem do gładzenia "na mokro", absolutnie niezbędne jest dokładne zapoznanie się z zaleceniami producenta konkretnego produktu, którego zamierzamy użyć – to on, znając skład chemiczny swojej masy, precyzuje, czy dany produkt nadaje się do tej metody i jakie są optymalne warunki oraz czasy aplikacji, co często jest kluczowe dla sukcesu. Na opakowaniu lub w karcie technicznej gładzi przeznaczonej do tej techniki często znajdziemy informację, że kolejną warstwę można nanosić po upływie zaledwie 1-3 godzin od aplikacji poprzedniej, a nie po kilkunastu, jak w metodzie tradycyjnej, kolejną warstwę gładzi można nanosić już w momencie, gdy pierwsza warstwa zmieniła kolor z ciemniejszego (mokrego) na jaśniejszy, ale wciąż jest "gumowata" w dotyku i daje się lekko zarysować paznokciem, ale nie odspaja się ani nie roluje pod naciskiem narzędzia. Ta minimalna przerwa technologiczna jest możliwa dzięki temu, że woda z nowo nakładanej warstwy może swobodnie dyfundować do wciąż wilgotnej warstwy spodniej, jednocześnie wspomagając jej dalsze wiązanie, a nie jedynie parować w powietrze; powoduje to powstanie silnego, trwałego wiązania międzywarstwowego, które często jest wytrzymalsze niż w przypadku nakładania na całkowicie suchą i przeszlifowaną powierzchnię, gdzie kluczowe jest jedynie mechaniczne zakotwiczenie nowego materiału i chemiczne wiązanie z powierzchnią. Główną zaletą metody "na mokro" jest oczywiście radykalne skrócenie czasu pracy – jeśli pierwsza warstwa potrzebuje 1-3 godzin do osiągnięcia odpowiedniej "wilgotności roboczej", a nałożenie drugiej warstwy trwa kolejne 2-3 godziny (w zależności od powierzchni i liczby osób pracujących), to teoretycznie w ciągu jednego dnia roboczego można nałożyć obie warstwy na znacznej powierzchni, podczas gdy w metodzie tradycyjnej same przerwy technologiczne wynoszą kilkanaście lub więcej godzin. Ponadto, metoda ta pozwala często uzyskać bardziej gładką powierzchnię bezpośrednio po nałożeniu drugiej warstwy, ponieważ nowo nakładany materiał niejako "scala" się z plastyczną powierzchnią spodniej warstwy, wypełniając nawet mikroskopijne nierówności i nie pozostawiając tak wyraźnych śladów narzędzia, co w efekcie minimalizuje (choć zazwyczaj nie eliminuje całkowicie) potrzebę późniejszego szlifowania, które jest najbardziej uciążliwym i pylącym etapem pracy.
Choć kusząca szybkością i efektem, metoda "na mokro" nie jest jednak panaceum i wymaga sporej wprawy. Wymaga perfekcyjnego wyczucia odpowiedniego momentu nałożenia drugiej warstwy – zbyt wcześnie, a materiał będzie się mazał, odspajał, tworzył pęcherze powietrza i zniszczycie pierwszą warstwę; zbyt późno, a właściwości "na mokro" przestaną działać i będziecie mieli trudność z równomiernym rozprowadzeniem materiału, a efekt będzie daleki od ideału. Nie każdy rodzaj gładzi nadaje się do tej techniki – są produkty dedykowane metodzie "na mokro", często z dodatkiem specjalnych polimerów, które zapewniają odpowiedni czas wiązania i elastyczność, a są też takie, które kategorycznie wymagają pełnego wyschnięcia i utwardzenia przed nałożeniem kolejnej warstwy, a próba ich zastosowania "na mokro" skończy się katastrofą i frustracją, a na końcu dodatkowymi kosztami związanymi z naprawą. Jest to technika, która bywa nieco bardziej agresywna dla podłoża w sensie dostarczania wilgoci, dlatego nie zawsze jest zalecana na materiały szczególnie wrażliwe na wodę (choć na płytach GK, które same w sobie są gipsowe i spoinowane produktami na bazie gipsu, metoda ta jest powszechnie stosowana z dobrym skutkiem). Wreszcie, błędy popełnione podczas aplikacji "na mokro" są trudniejsze do skorygowania od razu – jeśli coś pójdzie nie tak, często trzeba poczekać na całkowite wyschnięcie obu warstw (co trwa dłużej, bo są wilgotne) i dopiero wtedy szlifować lub nanosić kolejną, naprawczą warstwę, tracąc tym samym całą pierwotną przewagę czasową tej metody. Z tego względu, choć pozwala przyspieszyć prace wykończeniowe, metoda "na mokro" jest zazwyczaj domeną bardziej doświadczonych wykonawców, którzy potrafią precyzyjnie ocenić gotowość podłoża i materiału oraz pracować szybko i sprawnie, minimalizując ryzyko popełnienia błędu. Wykres obok prezentuje orientacyjne czasy oczekiwania między warstwami dla obu metod, ilustrując potencjalne oszczędności czasowe związane z techniką "na mokro", choć należy pamiętać, że są to wartości idealne i mogą się znacząco różnić w zależności od realnych warunków na budowie i specyfiki użytego materiału.
Przygotowanie pierwszej warstwy gładzi przed nałożeniem kolejnej
Etap przygotowania pierwszej warstwy gładzi przed nałożeniem kolejnej jest równie ważny, co samo jej nałożenie i decyduje w dużej mierze o ostatecznej jakości finiszu oraz trwałości całego systemu. Po wyschnięciu pierwszej warstwy, niezależnie od tego, czy stosowaliśmy tradycyjną gładź szpachlową do wyrównania większych nierówności czy finiszową do wstępnego wygładzenia, jej powierzchnia rzadko kiedy jest idealna – niemal zawsze widać na niej ślady pacy (tzw. "żeberka"), drobne nierówności, zgrubienia materiału na krawędziach, a także miejsca, gdzie materiał mógł się lekko skurczyć podczas wysychania, pozostawiając subtelne zagłębienia lub rysy. Standardową procedurą, zwłaszcza w metodzie "sucho na sucho", jest delikatne przeszlifowanie pierwszej warstwy, aby usunąć te najbardziej widoczne defekty – zazwyczaj używa się do tego papieru ściernego o gradacji P80 lub P100, co jest znacznie grubszą granulacją niż ta stosowana do finalnego szlifowania (gdzie dochodzi się do P180, P200 lub nawet wyżej), ponieważ celem nie jest tu osiągnięcie gładkości, lecz wyrównanie powierzchni i usunięcie "górek" oraz "dolinek" pozostałych po pierwszym przejściu, tworząc jednocześnie chropowatą fakturę, która poprawia przyczepność dla kolejnej warstwy. Niemniej jednak, w wielu przypadkach, szczególnie gdy pierwsza warstwa została położona bardzo starannie i ma niewielkie niedoskonałości, a czas goni, lub gdy planujemy zastosowanie metody "na mokro" lub nakładanie gładzi finiszowej która jest bardzo plastyczna, czynność szlifowania między warstwami jest często pomijana i wyrównuje się jedynie najbardziej rażące "górki" za pomocą pacy czy szpachelki, koncentrując się na bardzo dokładnym odpyleniu powierzchni, a właściwe szlifowanie i dążenie do ostatecznej gładkości odkłada się dopiero na moment po wyschnięciu drugiej, cieńszej i bardziej precyzyjnej warstwy, co generuje znacznie mniej pyłu i wymaga mniej pracy.
Decyzja o tym, czy szlifować pierwszą warstwę, zależy więc od jej jakości, stosowanej metody aplikacji kolejnej warstwy oraz preferencji wykonawcy, ale kluczowe jest, że jeżeli od wykonania pierwszej warstwy gładzi nie minęło więcej niż kilka dni (powiedzmy, do 7-10 dni, w zależności od warunków i typu gładzi), a powierzchnia ściany nie była szlifowana lub była jedynie lekko przetarta w celu usunięcia zadziorów i następnie starannie odpylona, z reguły nie ma konieczności ponownego gruntowania podłoża przed nałożeniem kolejnej warstwy. Dlaczego? Ponieważ pierwsza, świeża warstwa gładzi, o ile jest dobrze związana z podłożem i czysta, stanowi doskonałą bazę dla kolejnej warstwy; jej powierzchnia, nawet po lekkim szlifowaniu, wciąż posiada dobrą chłonność i przyczepność, a sam materiał jest na tyle "żywy", że chemicznie dobrze reaguje z nową, mokrą warstwą gładzi. Gruntowanie między świeżymi warstwami gładzi mogłoby w niektórych przypadkach nawet zaszkodzić – zastosowanie zbyt gęstego gruntu mogłoby stworzyć szklistą, niechłonną powłokę, która ograniczałaby przyczepność kolejnej warstwy, podczas gdy celem jest silne, jednolite wiązanie. Natomiast sytuacja zmienia się radykalnie, gdy pierwsza warstwa gładzi jest stara, zniszczona, była wielokrotnie szlifowana bez odpowiedniego odpylenia lub jest bardzo chłonna z natury (np. niektóre starsze typy gładzi wapiennych lub źle dobrane materiały). W takim przypadku, a także gdy od aplikacji pierwszej warstwy minęło wiele tygodni lub miesięcy, a powierzchnia zebrała sporo kurzu, brudu i osadów, gruntowanie staje się absolutnie niezbędne – powinno być wykonane za pomocą specjalistycznego gruntu głęboko penetrującego lub ujednolicającego chłonność, co wzmocni starą warstwę, zredukuje jej chłonność do odpowiedniego poziomu i zapewni solidne "zakotwiczenie" dla nowo nakładanej powłoki, zapobiegając jej odspajaniu czy spękaniom. Warto pamiętać, że gruntowanie podłoża przed nałożeniem gładzi, niezależnie od tego, czy to gruntowanie między warstwami czy na początku prac, to etap, który zawsze należy wykonywać na idealnie czystej i odpylonej powierzchni – kurz i pył są największym wrogiem przyczepności i nawet najlepszy grunt nie zrekompensuje zaniedbań w tym zakresie. Proces ten, choć pozornie prosty, wymaga metodycznego podejścia, dbałości o detale (np. staranne oczyszczenie narożników i trudno dostępnych miejsc) i często jest znacznie bardziej czasochłonny, niż mogłoby się wydawać komuś, kto nigdy tego nie robił, ale jest on fundamentem, na którym opiera się trwałość i estetyka ostatecznego wykończenia.