Ile Schnie Gładź Szpachlowa? Od Czego Zależy Czas Schnięcia
Czy istnieje coś bardziej nurtującego podczas prac remontowych niż niekończące się czekanie? Kładziesz gładź i jedyne, co zaprząta twoje myśli, to: "Ile schnie gładź szpachlowa"? To pytanie, równie powszechne, co kluczowe dla harmonogramu dalszych prac, nie ma niestety jednej, uniwersalnej odpowiedzi, ale ma swoją rzetelną ramy. Czas schnięcia gładzi szpachlowej zazwyczaj waha się od 6 do 24 godzin na jedną warstwę, choć jak zaraz się przekonacie, to tylko punkt wyjścia do bardziej złożonej dyskusji.
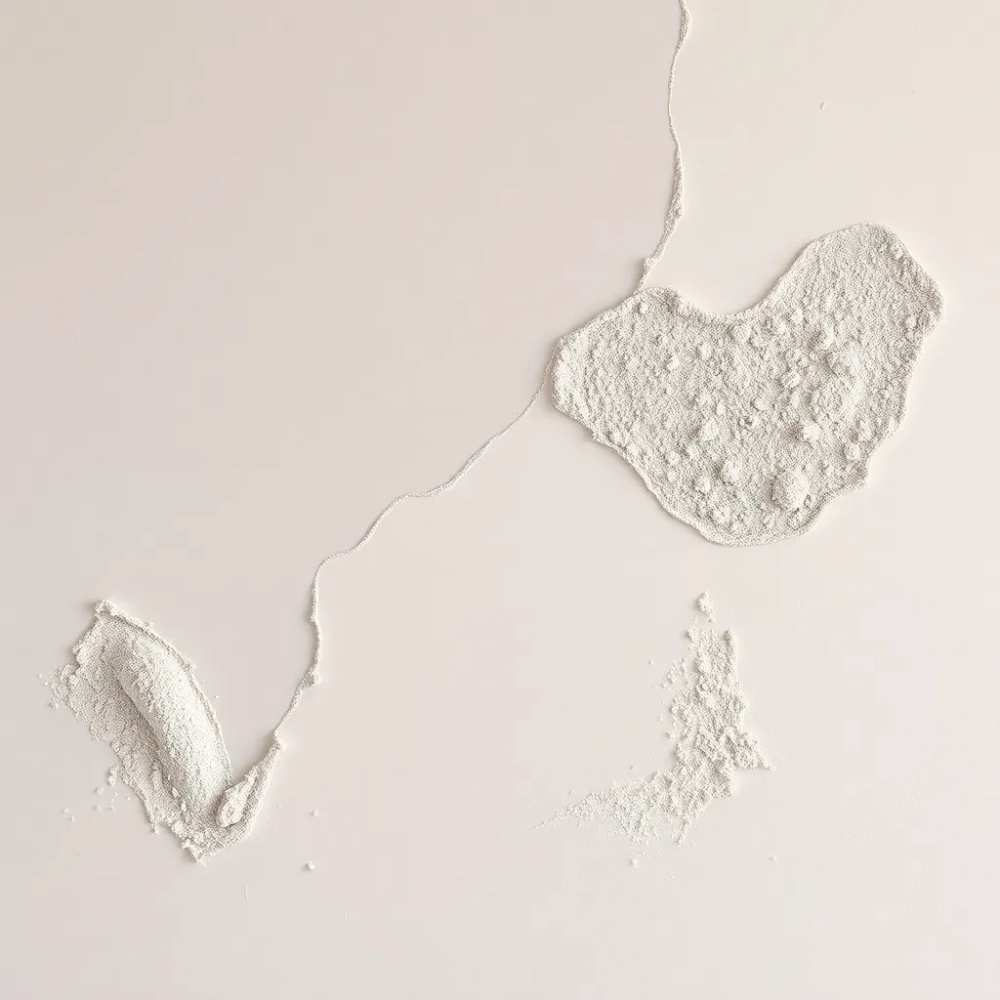
Precyzyjne określenie momentu, gdy gładź osiągnie gotowość do dalszych etapów obróbki, stanowi sedno planowania każdego przedsięwzięcia remontowego czy budowlanego. Wbrew pozorom, nie jest to kwestia jedynie teoretyczna, lecz ma bezpośrednie przełożenie na koszty, terminowość i ostateczny efekt wizualny powierzchni ścian oraz sufitów.
Analizując różne scenariusze i specyfikacje produktowe dostępne na rynku, szybko dochodzimy do wniosku, że "standardowe" ramy czasowe schnięcia to zaledwie ogólny zarys. Różnorodność materiałów, warunków aplikacji oraz czynników środowiskowych wprowadza znaczące odchylenia od tej średniej. Poniższa tabela przedstawia orientacyjne czasy schnięcia dla różnych typów gładzi i warunków, oparte na obserwacjach i danych technicznych.
Rodzaj Gładzi | Grubość Warstwy (mm) | Temperatura (°C) | Wilgotność Powietrza (%) | Wentylacja | Orientacyjny Czas Schnięcia (h) |
---|---|---|---|---|---|
Gotowa (akrylowa/polimerowa) | do 1 | 20-22 | 50-60 | Dobry przewiew | 6 - 10 |
Gotowa (akrylowa/polimerowa) | do 1 | 15-18 | 65-70 | Umiarkowany przewiew | 12 - 18 |
Sypka (gipsowa) | 2 - 3 | 20-22 | 50-60 | Dobry przewiew | 18 - 24 |
Sypka (gipsowa) | 2 - 3 | 15-18 | 65-70 | Umiarkowany przewiew | 24 - 36+ |
Sypka (cementowo-wapienna) | do 5 | 20-22 | 50-60 | Dobry przewiew | 48 - 72+ |
Sypka (gipsowa) | 5 - 8 (wypełnianie) | 20-22 | 50-60 | Dobry przewiew | 36 - 48+ |
Jak widać na przykładzie powyższych danych, prosta odpowiedź na pytanie "ile to schnie?" jest niemożliwa bez uwzględnienia kluczowych determinantów. Od wyboru materiału, przez precyzję jego aplikacji, aż po stworzenie sprzyjającego mikroklimatu w pomieszczeniu – każdy detal ma wagę. Szczególnie zastanawiające jest, jak ogromne różnice generują skrajne warunki, gdzie w optymalnej sytuacji mamy kilka godzin, a w niesprzyjającej nawet kilka dni oczekiwania.
Zrozumienie mechanizmów rządzących procesem twardnienia i wysychania gładzi pozwala nie tylko lepiej planować prace, ale także przewidywać potencjalne problemy i im zapobiegać. Przechodząc do szczegółowej analizy, zgłębimy każdy z tych czynników z osobna, dostarczając konkretnych danych i praktycznych wskazówek, które pozwolą uniknąć kosztownych pomyłek i przyspieszyć realizację projektu.
Rodzaj Gładzi a Czas Schnięcia
W świecie chemii budowlanej, gładź szpachlowa to nie jest po prostu "coś, co kładziemy na ścianę, żeby była gładka". Mamy do czynienia z szeroką gamą produktów, gdzie każdy typ ma swoje specyficzne właściwości, w tym decydujący wpływ na to, jak szybko schnie gładź. Zasadniczo, możemy podzielić je na kilka podstawowych kategorii, a różnice w ich składzie chemicznym i mechanizmach wiązania wody przekładają się bezpośrednio na tempo twardnienia i wysychania.
Na rynku dominują głównie gładzie gipsowe (sypkie i gotowe), gładzie polimerowe/akrylowe (gotowe) oraz, rzadziej w pracach wykończeniowych, cementowo-wapienne. Każda z tych kategorii ma swoje optimum zastosowań i, co najważniejsze dla naszego zagadnienia, swoje charakterystyczne czasy schnięcia, podyktowane naturą głównego spoiwa.
Gładzie gipsowe, najpopularniejsze do wnętrz, bazują na siarczanie wapnia. Po zmieszaniu z wodą (lub w przypadku gotowych, po prostu podczas ekspozycji na powietrze i utracie wody), gips przechodzi proces hydratacji, czyli wbudowuje cząsteczki wody w swoją strukturę krystaliczną, twardniejąc. Równolegle następuje odparowanie nadmiaru wody zarobowej. Czas schnięcia i twardnienia jest tu wynikiem sumy tych dwóch procesów.
Gotowe gładzie polimerowe lub akrylowe działają na nieco innej zasadzie – twardnieją głównie poprzez odparowanie wody z dyspersji polimerowej. Nie zachodzi tu tak intensywny proces chemicznego wiązania wody jak w przypadku gipsu czy cementu. Z tego powodu schnięcie gładzi gotowych jest zazwyczaj szybsze, zwłaszcza przy nakładaniu cienkich warstw, co czyni je wyborem preferowanym, gdy czas gra kluczową rolę.
W odróżnieniu od nich, gładzie cementowo-wapienne, stosowane głównie w pomieszczeniach o podwyższonej wilgotności jak łazienki czy piwnice, wymagają dłuższego czasu na wiązanie hydrauliczne spoiwa cementowego i karbonatyzację wapna. Procesy te przebiegają znacznie wolniej i wymagają odpowiedniej ilości wody do zajścia. Dlatego też ile schną gładzie na ścianie wykonane z mieszanek cementowo-wapiennych to często kwestia dni, a nawet tygodnia dla grubszych warstw, a nie godzin.
Weźmy przykład praktyczny. Ekipa remontowa miała do wyrównania ściany w starym budownictwie. Jedno pomieszczenie miało być salonem, drugie małą pralnią w piwnicy. Do salonu wybrali sypką gładź gipsową. Mieszali ją na bieżąco, kładąc dwie cienkie warstwy. Każda warstwa, przy dobrych warunkach (o czym później), schła około 18-20 godzin, co pozwoliło na szlifowanie i gruntowanie już następnego dnia. W pralni użyli gładzi cementowo-wapiennej. Tam musieli poczekać ponad 48 godzin na pierwszą warstwę, zanim mogli ocenić, czy potrzebna jest poprawka. Różnica była kolosalna w planowaniu kolejnych etapów.
Różnice w składzie chemicznym nie dotyczą tylko głównego spoiwa. Producenci dodają do gładzi szereg domieszek modyfikujących, takich jak opóźniacze lub przyspieszacze wiązania, środki zwiększające przyczepność, plastyfikatory czy też proszki redyspergowalne polimerów. Te ostatnie są powszechne w gotowych gładziach i znacznie poprawiają ich elastyczność oraz szybkość wysychania przez ułatwienie odparowania wody.
Gładzie sypkie gipsowe mają też różne klasy twardości i przyczepności (np. startowe, finiszowe), co również może wpływać na czas schnięcia. Gładź startowa, często grubsza i z większym uziarnieniem, może wymagać nieco więcej czasu na wyschnięcie grubszego ziarna niż drobniejsza gładź finiszowa, choć zasadnicza różnica leży w grubości warstwy i sposobie aplikacji.
Decydując się na konkretny rodzaj gładzi, warto dokładnie zapoznać się ze specyfikacją producenta. Często podają oni orientacyjny czas schnięcia jednej warstwy w optymalnych warunkach, np. "ok. 6-8h dla 1 mm warstwy w temp. 20°C i wilgotności 60%". To cenna wskazówka, choć jak wiemy, warunki "laboratoryjne" rzadko panują na placu budowy. Nie mniej jednak, producenckie karty techniczne są pierwszym miejscem, gdzie szukać rzetelnych danych.
Gotowe gładzie, ze względu na swoją wygodę i często szybsze tempo schnięcia cieńszych warstw, zyskały ogromną popularność w pracach wykończeniowych i remontowych. Ich cena jednostkowa (za kilogram czy wiadro) jest zazwyczaj wyższa niż gładzi sypkich, ale kompensuje to oszczędność czasu pracy (brak konieczności mieszania) oraz potencjalnie szybszy postęp całego projektu. Na przykład, typowe wiadro gotowej gładzi waży około 17-20 kg i kosztuje od kilkudziesięciu do ponad stu złotych, w zależności od jakości i producenta. Paczka gładzi sypkiej (np. 25 kg) kosztuje podobnie lub nieco mniej, ale wymaga nakładu pracy na przygotowanie zaprawy.
Wybierając gładź do konkretnego zastosowania, zawsze stajemy przed kompromisem między właściwościami materiału, kosztem, łatwością aplikacji i właśnie czasem schnięcia gładzi. Projekt w starej wilgotnej kamienicy może wymagać gładzi cementowo-wapiennej pomimo dłuższego schnięcia, ze względu na odporność na wilgoć. Szybki remont przed wprowadzeniem się najemców będzie faworyzował szybkoschnącą gładź polimerową.
Rozumiejąc te różnice, możemy świadomie dobierać materiały. Pomyłka na tym etapie może skutkować nie tylko dłuższym oczekiwaniem, ale też potencjalnymi problemami z trwałością powłoki malarskiej czy tapet. Niewystarczająco sucha gładź to prosta droga do spękań, odspojeń, a w skrajnych przypadkach nawet rozwoju pleśni pod warstwą wykończeniową. Diabeł tkwi w szczegółach i odpowiedni dobór gładzi to pierwszy, fundamentalny krok.
Niekiedy producenci oferują specjalistyczne gładzie szybkoschnące. Te produkty zawierają specjalne dodatki chemiczne, które przyspieszają proces wiązania spoiwa gipsowego lub odparowanie wody z dyspersji polimerowej. Ich stosowanie może skrócić czas oczekiwania o kilka, a nawet kilkanaście godzin w sprzyjających warunkach. Są to rozwiązania często droższe od standardowych produktów, ale w sytuacjach "awaryjnych" lub przy bardzo napiętym harmonogramie mogą okazać się wybawieniem, wartym poniesienia dodatkowych kosztów. Warto jednak zawsze czytać drobny druk – czas schnięcia tych "szybkich" gładzi nadal jest silnie zależny od temperatury i wilgotności.
Na przykład, testowaliśmy w redakcji pewną szybkoschnącą gładź gipsową, która według producenta miała być gotowa do szlifowania po 4-6 godzinach w temperaturze 23°C i wilgotności 55%. W realnych warunkach na budowie, przy temperaturze około 20°C i wilgotności 65%, czas ten wydłużył się do około 8-10 godzin. Nadal było to szybciej niż standardowe 18-24 godziny dla zwykłej gładzi sypkiej, ale pokazało, jak czynniki zewnętrzne potrafią zmodyfikować laboratoryjne dane. Ważne, by patrzeć na te liczby jako na wartości orientacyjne, a nie sztywne gwarancje.
Innym ciekawym przykładem są masy naprawcze do szybkich prac. Często bazują one na cementach portlandzkich błyskawicznych lub specjalnych polimerach. Potrafią twardnieć w ciągu kilkudziesięciu minut! Ale uwaga – to nie są typowe gładzie na całą ścianę, lecz raczej materiały do wypełniania dziur, ubytków czy osadzania narożników. Ich bardzo szybki czas wiązania wiąże się z trudniejszą aplikacją na dużych powierzchniach i często wymagają nałożenia tradycyjnej gładzi na wierzch dla uzyskania idealnie gładkiej faktury.
Podsumowując wątek rodzajów gładzi, świadomy wybór produktu, dostosowany do warunków panujących na budowie oraz specyfiki pomieszczenia (np. stopnia wilgotności), jest absolutnie fundamentalny. Nigdy nie zakładajmy, że "gładź to gładź". Każdy rodzaj ma swoje unikalne "tempo życia", a od naszego zrozumienia tego tempa zależy płynność i sukces całego przedsięwzięcia malarsko-wykończeniowego. Nie warto iść na skróty, wybierając gładź tylko ze względu na cenę, bez analizy jej właściwości, w tym oczywiście czasu schnięcia. Lepiej poświęcić chwilę na analizę specyfikacji, niż potem czekać w nieskończoność lub, co gorsza, borykać się z defektami na wykończonej powierzchni.
Decyzja o wyborze gładzi powinna być podyktowana analizą wielu czynników, ale czas schnięcia stanowi jeden z najistotniejszych, wpływając bezpośrednio na harmonogram projektu. Wiedza o tym, jak różne spoiwa i domieszki wpływają na ten proces, pozwala podejmować bardziej świadome decyzje na etapie zakupów i planowania pracy. Nie bójmy się pytać producentów i sprzedawców o detale dotyczące czasu schnięcia ich konkretnych produktów – w końcu to oni najlepiej znają swoje receptury i parametry, a taka wiedza jest bezcenna w praktyce remontowej. Pamiętajmy, że nawet najlepszy produkt może nie spełnić swojej roli, jeśli jego specyficzne "potrzeby" w zakresie schnięcia zostaną zignorowane.
Grubość Nakładanej Warstwy
Jeśli czas schnięcia gładzi szpachlowej byłby sportem ekstremalnym, to grubość warstwy byłaby jednym z głównych przeszkód na torze. Prosta zasada "im grubsza warstwa, tym dłużej schnie" wydaje się oczywista, ale jej praktyczne implikacje są często niedoceniane. Grubość ma potężny, wręcz wykładniczy wpływ na tempo wysychania, a nakładanie materiału w odpowiedni sposób jest sztuką, która bezpośrednio przekłada się na efektywność prac.
Wyobraźmy sobie warstwę gładzi jak mały zbiornik wody zamknięty od dołu przez ścianę. Woda musi odparować w górę, przez powierzchnię wystawioną na powietrze. Gdy warstwa jest cienka, cząsteczki wody mają krótką drogę do pokonania. Gdy warstwa jest gruba, woda z głębszych partii materiału musi przedostać się przez już schnącą (lub schnącą wolniej) wierzchnią warstwę, co znacznie utrudnia i spowalnia cały proces dyfuzji pary wodnej.
Co więcej, zbyt grube warstwy niosą ze sobą ryzyko, że wierzchnia warstwa wyschnie i zwiąże, tworząc twardą skorupę, podczas gdy materiał pod nią wciąż będzie wilgotny. Ta wewnętrzna wilgoć będzie uwięziona, co może prowadzić do szeregu problemów: wolniejszego schnięcia całości, zwiększonego ryzyka skurczu i pęknięć (szczególnie przy schnięciu gipsów), a nawet problemów z przyczepnością do podłoża czy kolejnych warstw. To klasyczny przypadek, kiedy chęć przyspieszenia procesu poprzez "jedno grube pociągnięcie" odnosi odwrotny skutek i prowadzi do niepotrzebnych opóźnień lub defektów.
Standardowa praktyka zaleca nakładanie gładzi w możliwie cienkich warstwach, zazwyczaj od 0.5 mm do maksymalnie 3-5 mm jednorazowo, w zależności od typu produktu i przeznaczenia. Gładzie finiszowe często nakłada się wręcz na grubość papieru, co umożliwia ich wyschnięcie w kilka godzin przy dobrych warunkach. Gładzie startowe lub szpachle do większych ubytków mogą być kładzione grubiej, ale zawsze w ramach limitów podanych przez producenta.
Konkretne dane? Jeśli warstwa gładzi gipsowej o grubości 2 mm schnie w optymalnych warunkach około 24 godzin, to warstwa o grubości 4 mm może schnąć nie 48, ale nawet 72 godziny lub dłużej. Zależność nie jest liniowa! Grubość 8 mm, która mogłaby wydawać się rozsądna do wypełnienia większego ubytku, może oznaczać czas schnięcia liczony w dniach, a nawet tygodniu, z ogromnym ryzykiem pęknięć.
Mistrzowie fachu doskonale wiedzą, że kluczem do szybkiej i trwałej gładzi jest praca etapowa. Zamiast próbować wyrównać znaczące nierówności (np. 1 cm) jedną, potwornie grubą warstwą gładzi, co jest błędem kardynalnym, lepiej jest zastosować materiał wypełniający przeznaczony do większych grubości (np. zaprawę tynkarską czy specjalną szpachlę do głębokich ubytków), a następnie przejść do dwóch lub trzech cienkich warstw gładzi, nakładanych po całkowitym wyschnięciu poprzedniej warstwy.
Przykład z życia wzięty: znajomy remontował starą ścianę, która miała znaczne zagłębienia po usunięciu listew przypodłogowych. Zamiast użyć szybkiej szpachli naprawczej, postanowił wypełnić te miejsca tą samą gładzią finiszową, którą miał wykańczać całą ścianę, kładąc warstwę grubości 1 cm w zagłębieniach. Minęły 3 dni, gładź na większości ściany była sucha, gotowa do szlifowania, ale te grube łaty nadal były wilgotne, a w niektórych miejscach zaczęły pojawiać się pęknięcia skurczowe. Musiał wszystko zeskrobać, poczekać aż podłoże całkowicie wyschnie, a następnie zastosować odpowiednią technikę – szpachlę szybkoschnącą w kilku cieńszych warstwach. Cała sytuacja opóźniła malowanie o prawie tydzień.
Prawidłowa technika aplikacji ma tu kluczowe znaczenie. Użycie pacy lub długiej pacy ze stali nierdzewnej pod odpowiednim kątem pozwala zebrać nadmiar materiału i pozostawić warstwę o optymalnej, jednolitej grubości. Chodzi o to, aby równomiernie rozprowadzić materiał na całej powierzchni, bez tworzenia "górek" i "dołków", które nie tylko utrudniają późniejsze szlifowanie, ale także wpływają na nierównomierne schnięcie – grubsze miejsca schną oczywiście dłużej.
W kontekście kosztów, nakładanie gładzi w zalecanych cienkich warstwach jest również bardziej ekonomiczne. Grubsza warstwa to większe zużycie materiału na metr kwadratowy. Gładzie nie są najtańszymi produktami, a każde zbędne wiadro czy worek zwiększają koszt remontu. Typowe zużycie gładzi finiszowej wynosi około 1 kg na metr kwadratowy przy warstwie 1 mm. Podwojenie grubości warstwy dwukrotnie zwiększa zużycie i koszt materiału, a czas schnięcia rośnie dużo bardziej niż dwukrotnie.
Producenci gładzi często podają maksymalną rekomendowaną grubość jednorazowej aplikacji w karcie technicznej produktu. Przekroczenie tych wartości to proszenie się o kłopoty. Nawet najlepsza gładź, zaaplikowana zbyt grubo, nie wyschnie prawidłowo w rozsądnym czasie i może rozwinąć wady. Zatem kluczem jest umiar i precyzja w aplikacji, a nie pogoń za natychmiastowym wyrównaniem dużej powierzchni jedną warstwą.
Istnieją specjalistyczne gładzie przeznaczone do nakładania grubszych warstw, tzw. gładzie naprawcze lub szpachle do ubytków. Mają one inną recepturę, często wzbogaconą o włókna zbrojące czy specjalne wypełniacze, które minimalizują ryzyko pękania przy grubszych aplikacjach. Nawet one mają jednak swoje ograniczenia dotyczące maksymalnej grubości jednorazowej warstwy (np. do 10 mm, 20 mm, a nawet więcej, w zależności od produktu) i również wymagają znacznie dłuższego czasu na wyschnięcie niż standardowe gładzie finiszowe kładzione na cieńsze warstwy.
Podczas prac remontowych warto zainwestować czas w dobre przygotowanie podłoża. Usunięcie starych, luźnych warstw, gruntowanie i wyrównanie większych nierówności przed nałożeniem właściwej gładzi pozwoli na jej aplikację w cieńszych warstwach, co z kolei przyspieszy schnięcie. Często poświęcenie dodatkowych kilku godzin na startowym etapie pracy procentuje później krótszym czasem oczekiwania i łatwiejszym szlifowaniem.
Jednolitość grubości jest równie ważna jak jej optymalna wartość. Nierównomierne rozłożenie materiału, nawet przy stosunkowo cienkiej warstwie, spowoduje, że miejsca grubsze będą schły dłużej. To może utrudnić decyzję o rozpoczęciu szlifowania – ryzykujemy uszkodzenie jeszcze niewystarczająco twardych partii lub nierównomierne szlifowanie powierzchni. Zatem nie tylko "jak cienko", ale i "jak równo" ma znaczenie.
Nauka precyzyjnego nakładania gładzi cienkimi, równymi warstwami to umiejętność, którą zdobywa się z doświadczeniem, ale można ją znacznie przyspieszyć, świadomie pracując nad techniką i korzystając z odpowiednich narzędzi (np. pacy weneckiej czy agregatów szpachlarskich, które pozwalają natryskiwać gładź pod odpowiednim ciśnieniem, uzyskując jednolitą powłokę).
Podsumowując, kontrola nad grubością nakładanej warstwy gładzi to jeden z najpotężniejszych czynników, którymi możemy sterować, aby wpływać na tempo jej schnięcia i jakość końcową. Zamiast próbować zaoszczędzić czas, kładąc jedną grubą warstwę, należy priorytetowo traktować aplikację cienkich, równych warstw. To podejście jest bardziej pracochłonne w samej aplikacji, ale zwraca się z nawiązką krótszym czasem schnięcia, mniejszym ryzykiem wad i ostatecznie szybszym przejściem do kolejnych etapów prac.
Temperatura, Wilgotność i Wentylacja: Warunki Idealne
Nawet najlepsza gładź, położona w idealnej grubości, będzie schnąć w ślimaczym tempie, jeśli warunki środowiskowe w pomieszczeniu nie będą sprzyjające. Trzy magiczne czynniki – temperatura, wilgotność powietrza i wentylacja – tworzą trio, które rządzi procesem wysychania gładzi. Zaniedbanie któregokolwiek z nich może dosłownie "zabić" postęp prac i doprowadzić do frustrującego czekania, a nawet problemów z jakością.
Zacznijmy od temperatury. Proces odparowania wody, który jest kluczowy dla schnięcia większości gładzi (szczególnie gotowych i gipsowych), jest silnie zależny od temperatury otoczenia. W cieplejszym powietrzu woda paruje szybciej. Producenci zazwyczaj podają, że optymalna temperatura do prac z gładzią i jej schnięcia to około 20°C. Utrzymanie temperatury w zakresie 18-25°C jest z reguły wystarczające do zapewnienia prawidłowego i stosunkowo szybkiego schnięcia.
Co się dzieje, gdy temperatura jest zbyt niska, powiedzmy poniżej 10°C? Procesy odparowania i wiązania chemicznego (w przypadku gipsów/cementów) drastycznie zwalniają. Czas schnięcia może wydłużyć się z kilkunastu godzin do kilku dni. Praca w nieogrzewanym budynku w chłodniejszych miesiącach bez zastosowania dodatkowego ogrzewania to gwarancja bardzo długiego oczekiwania na wyschnięcie gładzi szpachlowej. To klasyczny błąd, który widuje się często na placach budowy.
Z drugiej strony, zbyt wysoka temperatura, zwłaszcza w połączeniu z bardzo niską wilgotnością powietrza, również może być problemem. Szybkie, nierównomierne odparowanie wody może prowadzić do naprężeń w świeżej gładzi, powodując pękanie gładzi. Gładź potrzebuje czasu nie tylko na odparowanie wody, ale też na spokojne związanie i utwardzenie struktury. Idealne, łagodne warunki sprzyjają trwałości.
Drugi filar to wilgotność powietrza. Powietrze ma ograniczoną zdolność do pochłaniania pary wodnej. Im wyższa wilgotność w pomieszczeniu, tym mniej wilgoci z gładzi może odparować. To czysta fizyka. Gdy wilgotność osiąga wysokie wartości (np. powyżej 70-80%), proces schnięcia może praktycznie zatrzymać się, ponieważ powietrze jest już nasycone parą wodną i nie jest w stanie przyjąć jej więcej z gładzi.
Dlatego też, wilgotność powietrza powinna być monitorowana, zwłaszcza w pomieszczeniach, gdzie panuje duża wilgotność, np. w łazienkach, kuchniach czy w nowo wybudowanych, niewygrzanych budynkach. Producenci zazwyczaj zalecają wilgotność nie wyższą niż 60-70%. W praktyce, im bliżej 50%, tym lepiej i szybciej przebiega schnięcie.
Położenie gładzi w pomieszczeniu po tynkowaniu mokrym, bez odpowiedniego czasu na wyschnięcie tynków i pozbycie się wilgoci technologicznej, to murowany problem z schnięciem gładzi. Ściany nasiąknięte wodą będą oddawały wilgoć do powietrza, podnosząc jego wilgotność i spowalniając schnięcie każdej kolejnej warstwy. Czasami trzeba poczekać tygodnie lub miesiące, aż sam budynek "wydmuchnie" większość wilgoci, zanim prace wykończeniowe będą mogły ruszyć pełną parą.
Trzeci, równie ważny element układanki, to wentylacja. Nawet w pomieszczeniu o idealnej temperaturze i początkowo niskiej wilgotności, świeżo nałożona gładź zaczyna oddawać wilgoć do powietrza. Jeśli powietrze stoi w miejscu, jego wilgotność lokalnie wzrasta wokół ściany. Dobra wentylacja zapewnia wymianę tego nasyconego wilgocią powietrza na świeże, suchsze powietrze z zewnątrz (lub z innych części budynku), co umożliwia dalsze odparowanie wody z gładzi.
Otwarcie okien i drzwi, stworzenie lekkiego przeciągu (ale nie nawałnicy, o czym zaraz) to najprostszy sposób na poprawę wentylacji. Stosowanie wentylatorów pokojowych, które cyrkulują powietrze w pomieszczeniu, również znacząco przyspiesza proces, rozprowadzając wilgotne powietrze i ułatwiając jego wymianę z powietrzem mniej nasyconym parą wodną. To często niedoceniany, a bardzo efektywny sposób na skrócenie czasu schnięcia gładzi.
Opowiem historię z życia: podczas remontu niewielkiego mieszkania w bloku, pewnego razu gładź nałożona wieczorem wydawała się rankiem nadal dziwnie wilgotna, mimo że w poprzednich pokojach, przy tych samych produktach, wszystko szło jak po maśle. Co się stało? Okazało się, że z powodu lęku przed kradzieżą, robotnicy na noc zamykali okna i drzwi balkonowe "na cztery spusty". Powietrze stało, nasycając się wilgocią z gładzi, a jej schnięcie znacząco spowolniło. Po prostu musieliśmy zacząć zostawiać uchylone okna i drzwi wewnętrzne, aby stworzyć minimalny ruch powietrza. Efekt był natychmiastowy – schnięcie wróciło do normy.
Idealne warunki to zatem: temperatura w przedziale 18-25°C, wilgotność powietrza poniżej 65%, najlepiej w okolicy 50%, oraz stała, lekka cyrkulacja powietrza zapewniona przez wentylację grawitacyjną (kratki wentylacyjne) lub wymuszoną (uchylone okna, drzwi, wentylatory, system rekuperacji). Monitoring tych parametrów za pomocą prostego termometru i higrometru kosztującego kilkadziesiąt złotych może uchronić nas przed poważnymi opóźnieniami.
Szczególną uwagę należy zwrócić na prace prowadzone w okresach o wysokiej wilgotności zewnętrznej (np. deszczowa jesień) lub w pomieszczeniach naturalnie wilgotnych (piwnice, nieocieplone partery). W takich przypadkach zapewnienie odpowiednich warunków może wymagać użycia specjalistycznego sprzętu, takiego jak osuszacze powietrza, które aktywnie usuwają wilgoć z atmosfery, radykalnie przyspieszając schnięcie.
Co absolutnie zabronione? Nie kieruj bezpośrednio na świeżą gładź silnych nadmuchów gorącego powietrza z dmuchaw czy farelek. Może to spowodować, że wierzchnia warstwa wyschnie błyskawicznie i popęka, podczas gdy pod spodem wilgoć zostanie uwięziona. Agresywne suszenie niszczy strukturę gładzi i prowadzi do defektów. Lepsze jest lekkie, równomierne ogrzewanie pomieszczenia i delikatny ruch powietrza.
Podsumowując, stworzenie i utrzymanie optymalnych warunków klimatycznych w pomieszczeniu to inwestycja, która zwraca się wielokrotnie szybszym i prawidłowym schnięciem gładzi, a co za tym idzie, skróceniem całkowitego czasu remontu i minimalizacją ryzyka wystąpienia problemów z jakością wykończenia. Monitorowanie temperatury, wilgotności i zapewnienie ciągłej wentylacji to absolutna podstawa, o której nie można zapomnieć po nałożeniu ostatniej warstwy gładzi.
Jak Przyspieszyć Proces Schnięcia Gładzi?
Czekanie na wyschnięcie gładzi może być irytujące, szczególnie gdy gonią nas terminy. Chęć przyspieszenia tego etapu jest zrozumiała. Na szczęście istnieją metody, które pozwalają na bezpieczne skrócenie czasu schnięcia gładzi, ale kluczowe jest stosowanie ich z rozwagą, aby nie wywołać efektów odwrotnych do zamierzonych – pęknięć, odspojeń czy nierównomiernego twardnienia. Nie ma magicznej różdżki, ale jest nauka i doświadczenie.
Podstawowa zasada, którą warto sobie wbić do głowy, to wpływanie na schnięcie gładzi poprzez optymalizację warunków, a nie przez agresywne działanie bezpośrednio na materiał. Przypominamy o kluczowym trio: temperaturze, wilgotności i wentylacji. Manipulując tymi czynnikami w kontrolowany sposób, możemy znacząco przyspieszyć proces schnięcia.
Pierwszym i najprostszym sposobem jest zwiększenie temperatury w pomieszczeniu. Podniesienie temperatury z 15°C do 20-22°C może skrócić czas schnięcia o kilka, a nawet kilkanaście godzin, w zależności od typu gładzi i jej grubości. Można to osiągnąć poprzez włączenie ogrzewania w budynku lub, w przypadku pojedynczych pomieszczeń, użycie termowentylatorów lub nagrzewnic (elektrycznych lub na paliwo, ale z bezwzględnym wymogiem odprowadzenia spalin na zewnątrz, aby uniknąć podniesienia wilgotności). Pamiętaj: nie kieruj strumienia gorącego powietrza bezpośrednio na ścianę. Lepiej ogrzewać równomiernie całe pomieszczenie.
Równie skutecznym, a często nawet ważniejszym czynnikiem, jest obniżenie wilgotności powietrza. Jak wspomnieliśmy, gdy powietrze jest nasycone wilgocią, schnięcie ustaje. Użycie profesjonalnych osuszaczy kondensacyjnych lub adsorpcyjnych to potężne narzędzie do przyspieszania schnięcia. Osuszacz wyciąga wodę z powietrza, zbierając ją w zbiorniku lub odprowadzając wężem. Może to skrócić czas schnięcia z kilku dni do kilkunastu godzin, zwłaszcza w wilgotnych pomieszczeniach lub po tynkach mokrych.
Na przykład, w piwnicy z naturalnie wysoką wilgotnością 80%, położenie gładzi w optymalnej grubości może oznaczać schnięcie trwające tydzień. Ustawienie średniej klasy osuszacza (np. o wydajności 20-30 litrów na dobę) w takim pomieszczeniu i praca nim przez 2-3 dni może skrócić ten czas do 24-36 godzin, oczywiście przy założeniu jednoczesnej wentylacji i odpowiedniej temperatury.
Trzeci filar to wentylacja – i tu jest sporo do zrobienia. Ciągła wymiana powietrza, nawet jeśli nie wprowadzamy suchego, gorącego powietrza z zewnątrz (co może być trudne np. zimą), pomaga usuwać nagromadzoną przy powierzchni ściany wilgoć. Otwarcie okien na tzw. "mikrouchył" czy stworzenie delikatnego przeciągu poprzez otwarcie drzwi w różnych częściach mieszkania to proste i darmowe metody. Lepszą kontrolę daje użycie wentylatorów pokojowych lub budowlanych (ale bez silnego nawiewu bezpośrednio na ścianę!), które wprawiają powietrze w ruch i wymuszają jego cyrkulację.
Przykład: pokój o wymiarach 4x5m (20m2). Po położeniu gładzi w temperaturze 18°C i wilgotności 70%, bez wentylacji, gładź schnie wolno. Otwarcie jednego okna na uchylanie i drzwi wewnętrznych do korytarza z wentylacją grawitacyjną znacząco przyspieszy ten proces. Dodanie wentylatora kierującego strumień powietrza ukośnie na ścianę (nigdy prostopadle!) może skrócić czas schnięcia gładzi szpachlowej nawet o 30-50% w porównaniu do braku wentylacji.
Czwarta, ale równie ważna strategia to kontrolowana, racjonalna technika nakładania. Stosowanie cieńszych warstw gładzi, o czym mówiliśmy wcześniej, jest samo w sobie potężnym sposobem na przyspieszenie procesu. Lepiej położyć dwie cienkie warstwy z krótkimi przerwami na schnięcie, niż jedną grubą, która będzie schła w nieskończoność. Prawidłowe przygotowanie materiału – unikanie nadmiernego rozcieńczenia gładzi sypkiej wodą – również przyspiesza schnięcie.
Piątą metodą jest, o ile to możliwe, zastosowanie szybkoschnących odmian gładzi, które chemicznie przyspieszają wiązanie. Są droższe, ale dla konkretnych projektów, gdzie czas jest absolutnym priorytetem, mogą stanowić opłacalne rozwiązanie. Należy jednak upewnić się, że ich użycie jest uzasadnione specyfiką pracy i budżetem. Czasem kilkadziesiąt złotych więcej na worek czy wiadro gładzi zwróci się skróceniem czasu pracy całej ekipy o dzień.
Warto wspomnieć o farbach gruntujących przyspieszających schnięcie, które stosuje się między warstwami gładzi lub przed pierwszą warstwą na chłonnych podłożach. Takie grunty szybko wnikają w podłoże lub delikatnie usztywniają wierzchnią warstwę schnącej gładzi, co może pośrednio pomóc w jej dalszym wysychaniu. Ale to raczej wsparcie, a nie główny motor napędowy przyspieszenia schnięcia.
Przy próbie przyspieszenia procesu kluczowe jest ciągłe monitorowanie stanu gładzi. Gładź gotowa jest sucha, gdy zmienia kolor z ciemniejszego, wilgotnego, na jaśniejszy, suchy, i gdy po przetarciu dłonią pozostawia charakterystyczny biały, pylisty ślad. Gładź sypka jest sucha, gdy jest całkowicie jednolita kolorystycznie i twarda – paznokieć nie powinien jej łatwo wbić. Wszelkie ciemniejsze plamy sugerują, że materiał jest w tych miejscach nadal wilgotny i wymaga dalszego schnięcia.
Pamiętajmy, że pośpiech jest złym doradcą. Agresywne, zbyt szybkie suszenie może doprowadzić do spękań, odspojeń od podłoża, a nawet do sytuacji, w której wewnętrzna warstwa gładzi nie wyschnie nigdy prawidłowo, prowadząc do defektów powłoki malarskiej lub tapety w przyszłości. Nierównomierne schnięcie to także nierównomierne twardnienie, co utrudni, a nawet uniemożliwi prawidłowe szlifowanie powierzchni.
Podsumowując, przyspieszanie schnięcia gładzi to głównie optymalizacja warunków – podniesienie temperatury, obniżenie wilgotności i intensyfikacja wentylacji, zawsze w sposób kontrolowany i umiarkowany. Dodatkowo, świadome stosowanie cienkich warstw i dobór materiałów (jeśli budżet na to pozwala) mogą być bardzo pomocne. Kluczem jest zachowanie zdrowego rozsądku i nieprzekraczanie granic bezpiecznych dla materiału, tak by szybciej znaczyło również lepiej i trwalej. Czasem lepiej poczekać kilka godzin dłużej, niż potem borykać się z kosztownymi i pracochłonnymi poprawkami. Kontrolowane przyspieszenie to finezja, a nie brutalna siła.